이번 글 부터 본격 8대공정 시작. 😊👆🏻
👇🏻👇🏻아래는 반도체 산업의 생태계를 다룬 내용이다.👇🏻👇🏻
진짜 하루만에 이해하는 반도체 산업 - Part3 반도체 산업의 생태계와 8대 공정
Part2에 이어, Part3에서는 반도체 산업의 생태계와 반도체 8대 공정이 다루어진다. 내용이 길어서 본 글은 반도체 산업 생태계 먼저 정리해 보았다. 👇🏻👇🏻아래는 앞선 메모리반도체 정리 링
dudwolog.tistory.com

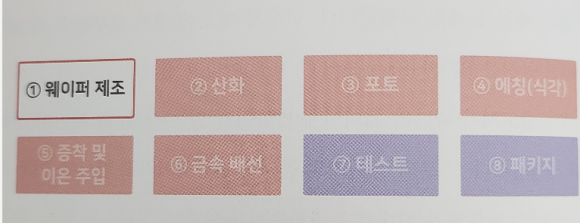
1. 웨이퍼 제조 공정
반도체8대공정중 가장 첫번째 공정인 웨이퍼제조공정은 IDM이나 파운드리 기업의 반도체 제조 시설에서 이뤄지지 않는다.
반도체 웨이퍼만을 전문적으로 생산하는 업체들이 따로 있어서 IDM이나 파운드리 기업이 구입해 사용한다.
1.웨이퍼의 재료, 실리콘 Si
실리콘은 지구의 지각을 구성하는 물질 중 27.7%를 차지하는 원소로 값이 싸고 쉽게 구할 수 있다. 주변에서 흔히 볼 수 있는 모래에도 실리콘이 포함되어 있다. 또, 원하는 영역에만 전기를 흐를 수 있도록 조절하기 쉽고, 안정된 구조의 절연 산화막을 형성할 수 있다. 녹는점이 높아 고온의 반도체 공정에 사용 가능하다는 것도 큰 장점. 이런 이유로 웨이퍼를 제조할 때 실리콘이 사용 됨.
2.실리콘 원자들을 규칙적으로 배열하기
1,800'C의 고온에서 모래로부터 나온 이산화규소(SiO2)와 탄소(C)를 반응시켜 순도 99%짜리 금속 급 실리콘, MGS(Metallurgical Grade Silicon)를 만든다. 99%면 충분하다고 생각할 수 있지만 웨이퍼의 재료로 쓰기에는 아직 불순물이 많다. 2차 정제 과정을 거치고 나서야 비로소 순도 99.999999%정도되는 전자 소자 급 실리콘, EGS(Electronic Grade Silicon)를 얻을 수 있다. 여기서 끝 아님. EGS의 실리콘 원자 배열이 고르지 않다는 문제가 있다.
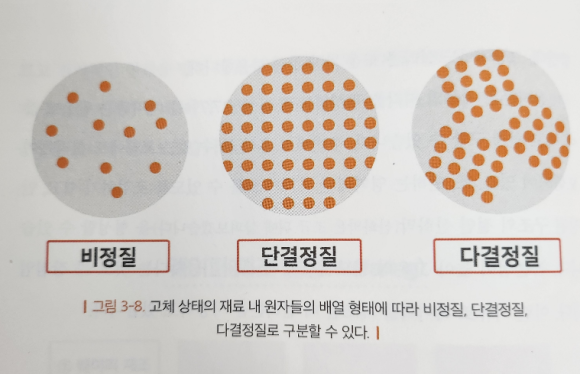
그림과 같이 EGS는 다결정질 상태인데 반도체마다 동일한 특성을 갖게 하기 위해서는 단결정질 상태로 만들어야 한다. 다결정질 실리콘을 단결정질 실리콘으로 만드는 방법으로는 초크랄스키법 (CZ법) 이 대표적이다. 부서진 초콜릿 조각들을 냄비에 모아 녹인 후 다시 굳혀서 하나의 의덩어리로 만드는 것과 비슷하다.
먼저, EGS 덩어리들과 붕소(B), 인(P), 비소(As)등의 도핑 원소를 함께 넣고 약 1,500'C 이상의 온도로 가열해 액체로 만든다. 이후, 실리콘 결정의 씨앗 역할을 하는 시드(Seed)를 줄 끝에 매달아 액체 상태의 실리콘 표면에 콕 찍어 접촉시킨다. 시드를 회전시키면서 천천히 위로 끌어올리면 액체 실리콘이 시드를 따라 천천히 굳어지며 단결정질 실리콘덩어리가 길게 만들어진다. 이 실리콘 덩어리를 잉곳 (Ingot)이라고 부른다.
실리콘 잉곳을 만드는 과정은 시드를 액체 실리콘 표면에 접촉시키는 찍기(Dipping), 잉곳의 품질을 결정하는 잉곳 목 뽑아내기(Necking), 원하는 직경까지 몸집을 불리는 어깨 만들기(Shouldering), 원하는 직경을 유지하면서 성장시키는 몸통성장(Body Growth), 성장을 마무리하는 꼬리 리만들기(Tailing) 순서로 진행된다. 여기서 잉곳의 상품성을 결정하는 단계는 '어깨만들기'와 '몸통성장'이다. 이 곳에서 잉곳의 직경 즉, 웨이퍼의 직경이 결정되기 때문.
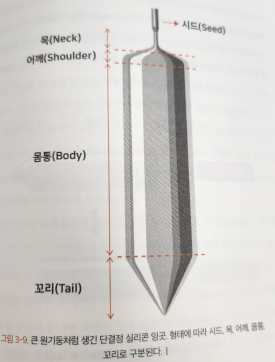
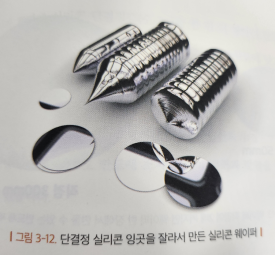
3.실리콘 잉곳을 잘라서 실리콘 원판으로 만들기
잉곳이 만들어진 후에는 직경이 균일하지 않아 상품성이 없는 목, 어깨, 꼬리를 제거한다. 몸통 이외의 다른 부분을 제거하는 것을 트리밍(Trimming)이라고 한다. 잉곳의 몸통은 커다란 원기둥 형태이지만, 실리콘 웨이퍼는 얇은 원판 형태이다. 이 원통을 얇게 썰어서 원판의 형태로 만들어야 한다. 이 공정이 소잉(Sawing)이다.
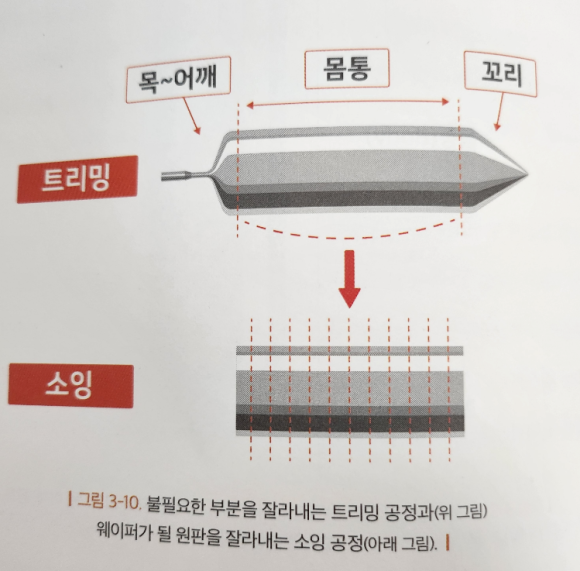
이때 다이아몬드 가루가 붙어있는 쇠줄인 와이어를 톱으로 사용하는데 와이어가 두꺼울수록 소잉 공정에서 손실되는 실리콘이 많아지므로 최대한 얇은 와이어를 사용하는 것이 관건이다.
4.실리콘 원판을 실리콘 웨이퍼로 만들기
성장할 땐 결함 없는 단결정이었던 실리콘 잉곳의 몸통은 소잉 공정을 거치면서 실리콘 원판 표면의 결정성이 손상되는 결정결함 이 발생하고, 가장자리 부분은 결정 결함이 많은 직각 모양을 갖게 된다. 이 상태에서는 가장자리에 가해지는 작은 충격에도 쉽게 깨질 수 있다. 그래서 소잉 공정이 끝난 실리콘 원판 가장자리를 둥글게 만들어주는 엣지라운딩 (Edge Rounding) 공정을 진행해 깨질 확률을 낮춰준다.
다음으로는 울퉁불퉁한 표면을 고르게 갈아주는 래핑 (Lapping) 공정을 진행한다. 하지만 표면을 물리적으로 갈아내는 과정에서 결정 결함이 발생하기 때문에 손상된 결정이 여전히 표면에 남아 있다. 그래서 표면의 손상된 결정을 화학적 방식으로 녹여서 제거하는 에칭 공정을 진행한다. 에칭이 끝나면 표면의 결정 결함 부위는 거의 다 사라진다. 하지만 원자 단위로 보면 아직도 표면이 울퉁불퉁하다. 그래서 원판 표면을 원자 단위에서 평탄하게 만들어주는 폴리싱 공정을 진행한다. 래핑은 물리적으로만 표면의 단차를 제거하지만, 폴리싱은 화학적 반응과 물리적 제거를 동시에 활용해 결정 결함을 만들지 않으면서 더 정밀하게 표면의 단차를 없앨 수 있다. 이렇게 제작된 실리콘 웨이퍼를 연마웨이퍼 (Polished wafer)라고 한다. 이렇게 실리콘 웨이퍼 표면을 평평하게 만드는 과정이 매우 중요하다. 반도체의 성능과 정밀도에 지대한 영향을 미치기 때문.
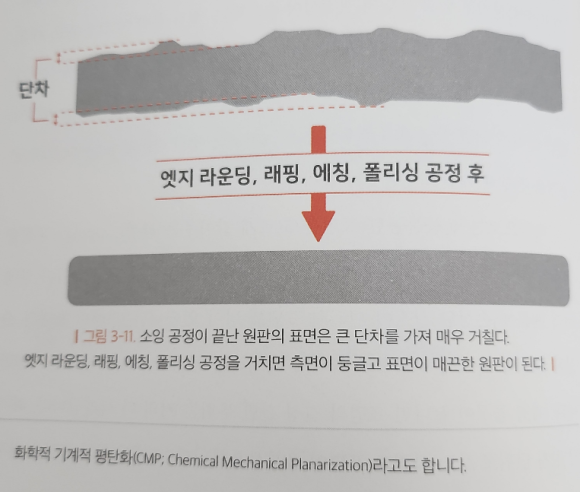
5.실리콘 웨이퍼의 발전 방향
실리콘 웨이퍼는 면적을 넓히는 방향으로 발전해왔다. 면적이 넓을수록 만들 수 있는 반도체 제품 개수가 늘어나기 때문.
1960년대 20 mm -> 1970년대 100mm -> 1980년대 150mm -> 1990년대 200mm
2000년대 300mm 로 점차 커졌다.
직경이 커졌는데 두께가 그대로라면 얇고 흐느적거리기 때문에, 직경이 커질수록 웨이퍼의 두께 또한 두꺼워진다. 300mm 웨이퍼는 775마이크로미터 두께로 가공되고 있다.
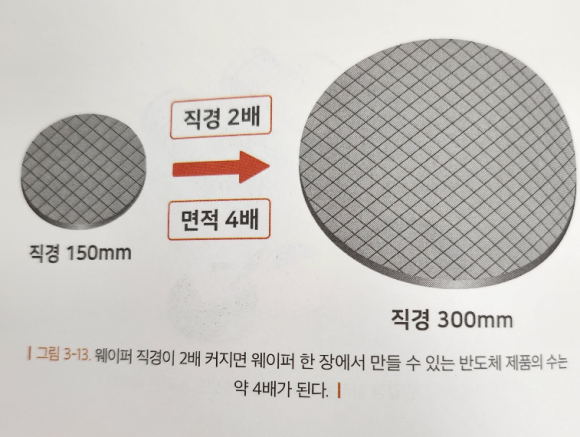
실리콘 웨이퍼의 직경에 따른 두께는 표준화되어 있어서 특수한 경우가 아니라면 대부분 회사에서 모두 동일 규격으로 생산한다. 현재 반도체 시장에서는 300mm 직경 웨이퍼가 계속 쓰이고 있다. 이 직경으로도 충분한 수의 실리콘 칩을 제작할 수 있기 때문.
반도체 성능이 발전하면서 더 좋은 실리콘 웨이퍼에 대한 수요가 늘고 있다. 이에 발맞춰 고부가가치의 웨이퍼들도 속속 등장하고 있다. 대표적으로 에피웨이퍼(Epitaxial Wafer)가 있다. 연마 웨이퍼표면에 실리콘 단결정층(수 마이크로미터)을 한번 더 쌓아서 만든 웨이퍼이다.
연마 웨이퍼에 비해 결정 결함이 적어 반도체 불량률이 낮고 단결정 층 두께를 유연하게 조절하여 다양한 용도에 맞춤 제작이 가능하다는 장점이 있다. 일부 특수 분야에서는 SOI웨이퍼 (Silicon On Insulator Wafer)가 사용된다. SOI웨이퍼는 두 개의 실리콘 층 사이에 산화막이 샌드위치처럼 끼어들어 있는 구조로 반도체 소자의 소비 전력과 발열을 낮출 수 있다는 장점이 있다.
'반도체공부' 카테고리의 다른 글
진짜 하루만에 이해하는 반도체 산업 - Part3 8대 공정 3. 포토공정 (1) | 2023.09.06 |
---|---|
진짜 하루만에 이해하는 반도체 산업 - Part3 8대 공정 2. 산화공정 (0) | 2023.09.04 |
진짜 하루만에 이해하는 반도체 산업 - Part3 반도체 산업의 생태계와 8대 공정 (0) | 2023.09.01 |
진짜 하루만에 이해하는 반도체 산업 - Part2 메모리반도체 (0) | 2023.08.31 |
진짜 하루만에 이해하는 반도체 산업 - Part2 시스템반도체 (2) | 2023.08.30 |