지난 시간부터 본격 반도체 8대공정 시작하였다.
👇🏻👇🏻아래 링크는 웨이퍼공정 공부👇🏻👇🏻
진짜 하루만에 이해하는 반도체 산업 - Part3 8대 공정 1. 웨이퍼제조공정
이번 글 부터 본격 8대공정 시작. 😊👆🏻 👇🏻👇🏻아래는 반도체 산업의 생태계를 다룬 내용이다.👇🏻👇🏻 진짜 하루만에 이해하는 반도체 산업 - Part3 반도체 산업의 생태계와 8대 공정
dudwolog.tistory.com
산화공정 Oxidation
1.전기를 차단하는 완벽한 방법, 산화막
실리콘이 산소와 만나면 산화 반응에 의해 이산화규소 SiO2 가 만들어진다. 이는 산화막을 만드는 데 활용된다. 반도체는 전류의 흐름을 통해 0과 1을 오가며 연산을 수행한다. 전기가 흐르는 곳과 흐르지 않는 곳을 확실하게 구분(절연)해줘야 하기 때문에 전류가 올바른 회로로만 흐를 수 있도록 반도체 소자 내에서, 또 반도체 소자 간에 차단벽을 세운다. 이렇게 차단벽의 역할을 하는 것이 산화막이다. 이산화규소를 활용해 산화막을 만드는 공정을 산화공정이라고 한다.
산화공정을 위해서는 세가지 준비물이 필요하다.
- 실리콘원자(웨이퍼에서 얻을 수 있다.),
- 산소원자(기체형태로 웨이퍼에 공급해줌),
- 열 에너지(실리콘 원자와 산소가 반응하도록 충분한 열 에너지-고온)
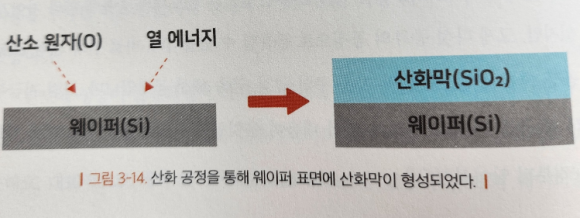
2. 다양한 곳에서 쓰이는 이산화규소
이산화규소는 절연층으로써 다양한 곳에서 활용된다. 하나의 반도체 안에는 수많은 MOSFET 소자가 들어가며, MOSFET소자 간 절연을 위한 이산화규소절연막 이 필요하다. 이 절연막을 STI (Shallow Trench Isolation)이라고 부른다. 웨이퍼 표면에는 반도체 소자들이 빼곡하게 채워져 있다. 이 표면에 전선을 배치하면, 전기적 연결이 잘못 형성되어 제대로 동작하지 않을 수 있다.
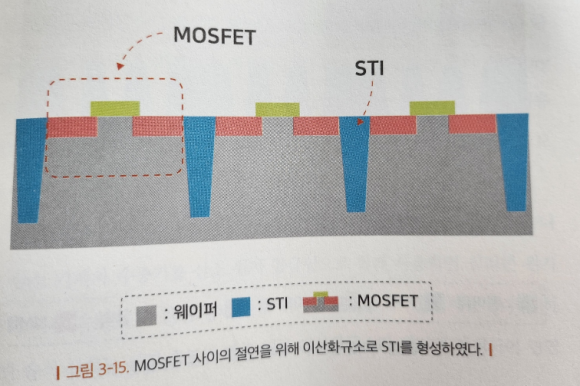
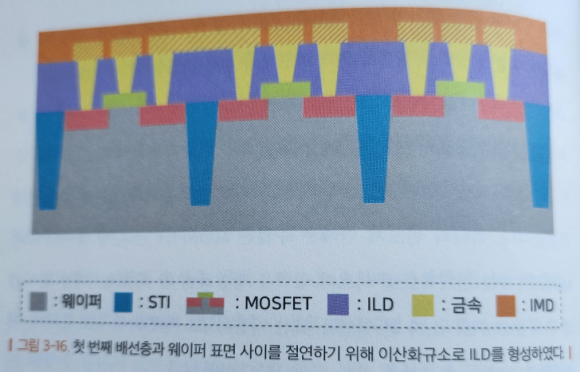
그래서 전선을 새로운 층으로 만들어 반도체 소자 위쪽으로 쌓아야 하는데, 이를 배선층 이라고 한다. 반도체 소자 위층에 생긴 첫번째 배선층(위 그림의 빗금 영역)과 웨이퍼 표면을 절연하기 기위한 이산화규소 절연막이 필요하고, 이를 ILD (Inter-Layer-Dielectric)라고 한다. ILD는 층간 절연뿐 아니라 소자의 전극(MOSFET이라면, 소스,드레인,게이트) 간의 절연역할도 한다.
복잡하게 설계된 회로를 한정된 면적 내에 구현하기 위해서는 더 많은 배선층이 있어야 한다.
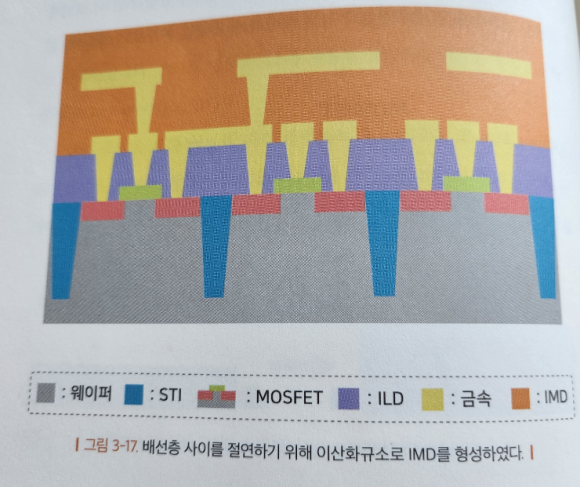
배선층 사이에도 절연을 해줘야 하며, 이때 사용하는 이산화규소 절연막을 IMD (Inter-Metal-Dielectric)라고 부른다.
3. 산화방식의 종류 (건식산화와 습식산화)
- 건식산화 : Dry Oxidation. 산소기체만을 이용해 산소원자를 공급. 산화막성장속도가 느린만큼 이산화규소의 밀도가 높게 형성되어 절연특성이 뛰어나다. 얇은두께유지
- 습식산화 : Wet Oxidation. 산소기체와 더불어 수증기(H2O)를 함께 사용하여 공급. 산화막성장속도는 건식산화막보다 5~10배 더 빠르다. 산소기체와 수증기를 산소원자 공급원으로 함께 사용하면 실리콘 원자에 더 빠른 속도로 더 많은 양의 산소원자를 공급할 수 있기 때문이다. 하지만 성장속도가 빠른만큼 이산화규소가 성기게 형성되면서 절연능력이 떨어진다.
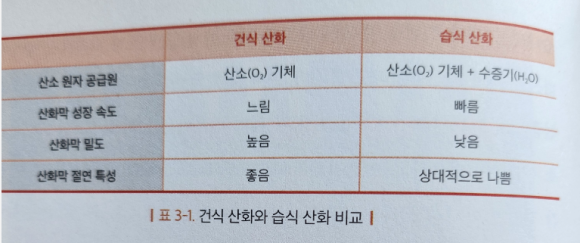
이러한 차이 때문에 두 방식으로 형성된 산화막은 활용도가 다르다.
'반도체공부' 카테고리의 다른 글
진짜 하루만에 이해하는 반도체 산업 - Part3 8대 공정 4. 에칭공정 (2) | 2023.09.09 |
---|---|
진짜 하루만에 이해하는 반도체 산업 - Part3 8대 공정 3. 포토공정 (1) | 2023.09.06 |
진짜 하루만에 이해하는 반도체 산업 - Part3 8대 공정 1. 웨이퍼제조공정 (1) | 2023.09.03 |
진짜 하루만에 이해하는 반도체 산업 - Part3 반도체 산업의 생태계와 8대 공정 (0) | 2023.09.01 |
진짜 하루만에 이해하는 반도체 산업 - Part2 메모리반도체 (0) | 2023.08.31 |